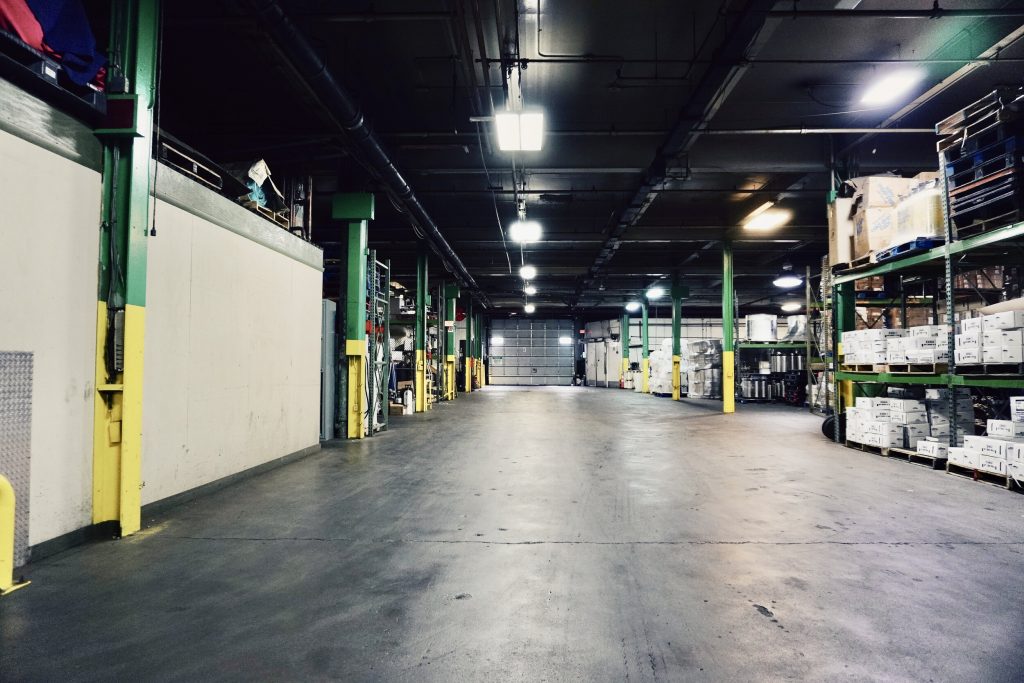
Our 90,000 square foot plant uses no natural gas, propane or fuel oil. Rather, we developed a highly efficient process whereby we reclaim heat from our ice manufacturing compressors to heat the entire building.·
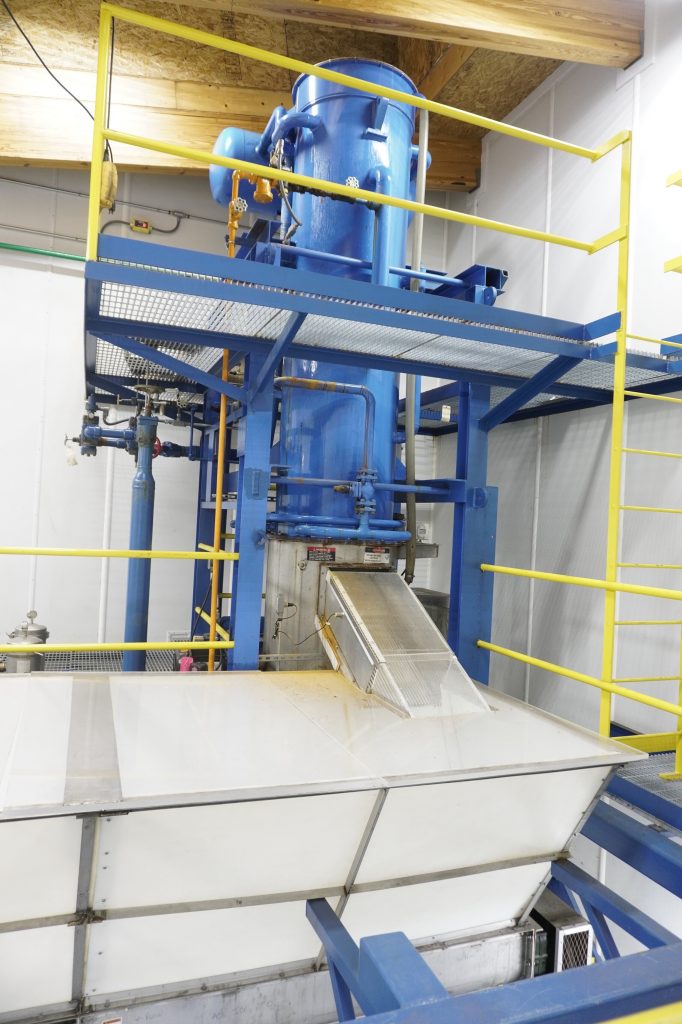
Each ice cube manufactured starts within one of our highly efficient Vogt ice makers, using top-grade water. Unlike our competitors, we don’t use reverse-osmosis — a process that wastes between 1.6 and 2.7 gallons of water to produce 1 gallon of pure water.
There’s more green to see with us beyond our logo.
Environmental Commitment. We believe success starts with good citizenship. With every major decision made, we weigh the environmental and energy-efficiency impacts. Some examples:
Unlike our competitors, we don’t use reverse-osmosis for ice manufacturing — a process that wastes between 1.6 and 2.7 gallons of water to produce 1 gallon of pure water.
We use top-grade water that originates in Minnesota’s Northern Woods. Minneapolis has been listed for many years as one of the Top 10 municipalities for clean water.
Ace Ice has invested heavily in metal detection to avoid product recalls, which waste water, packaging, labor and electricity.
Our state-of-the-art ice-making process — the most environmentally friendly for the industry — uses roll stock to drastically reduce waste. Heat sealing avoids using metal or plastic closing devices.
Unlike many ice manufacturers who “frost” their ice bags, Ace Ice uses clear bags — not only so customers see the product but also to reduce the amount of printed ink, which is harder to dispose.
Our 90,000 square foot plant uses no natural gas, propane or fuel oil. Rather, we developed a highly efficient process whereby we reclaim heat from our ice manufacturing compressors to heat the entire building.·
As an “Xcel Primary Energy User” we purchase only “raw” power, then convert it to useable power. This reduces waste and overhead – savings we can pass on to customers.
If the surrounding community needs additional power, Xcel will call on us to decrease our usage. We can shut down 100% for 6-10 hours by depending on our well-insulated facilities and backup energy source — a water-cooled, low RPM generator.
We conserve energy by using glycol-refrigerated cold plates inside most of our delivery trucks. Electricity is used only during non-delivery hours to rejuvenate the freezers.
Our monitoring system tracks how delivery personnel drive — how fast, how quickly they accelerate, decelerate, etc. Not only does this system monitor driver safety, it also provides data for fuel efficiency.
All trucks are turned off during delivery to conserve fuel.
All tires are checked daily on delivery vehicles to ensure optimum fuel efficiency.